Customized Training Builds Competitive Edge
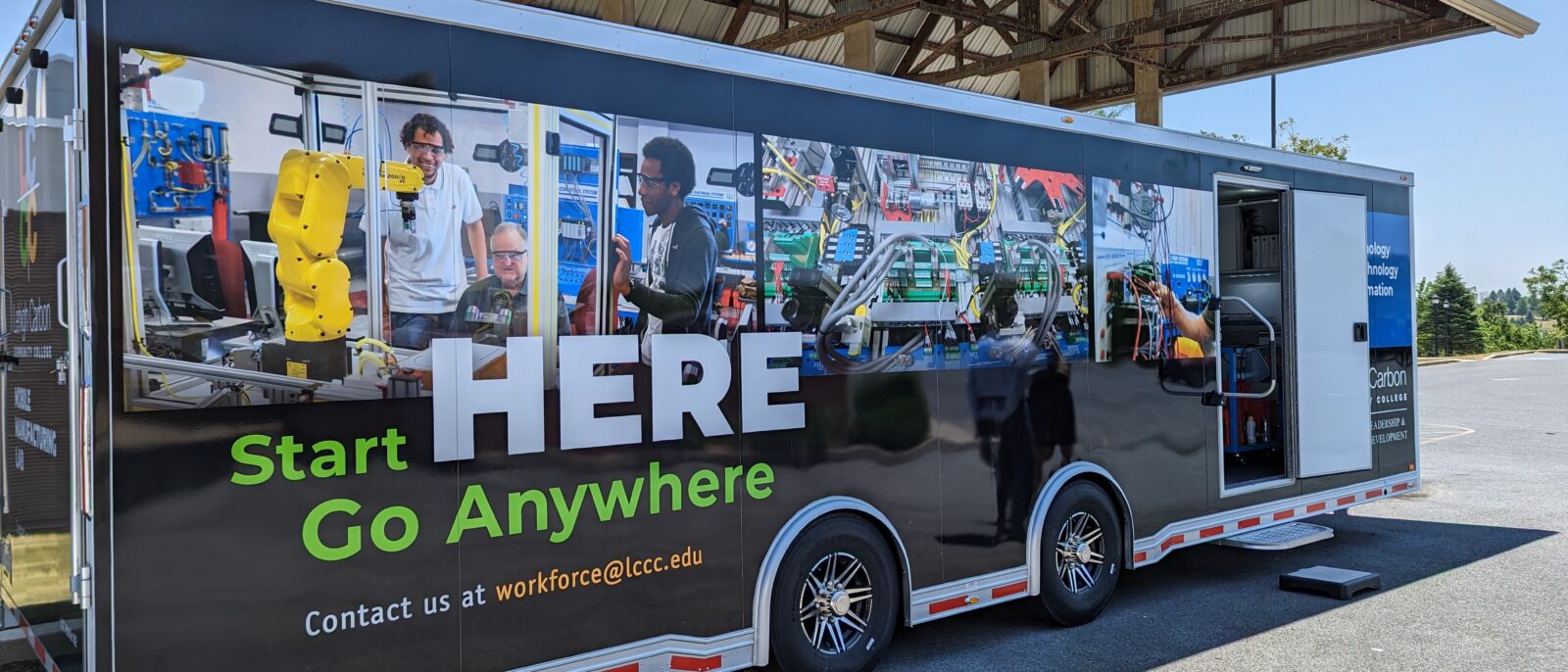
The surface of an office desk, the seat fabric in a car, laminates that mimic wood and stone; all are manufactured by Omnova North America, Division of Surteco. The company, headquartered in Germany, with a plant located in Auburn, is known worldwide for providing a diverse array of coated and engineered fabrics and laminates for everything from the marine and RV industries to electronics and corporate office spaces. Some of its notable clients include Walmart, Burger King and Subway. When it came time for employees at the Auburn plant to be trained, Omnova turned to Lehigh Carbon Community College. “We sent our team to LCCC for basic pneumatics, basic hydraulics and pneumatic troubleshooting on campus in 2023,” says Sarah Sarlat, maintenance planner scheduler at Omnova.
For companies like Omnova, A Division of Surteco, looking to train employees on-site, LCCC’s mobile manufacturing lab fits the bill perfectly. The state-of-the-art lab is accessible for electro mechanical technicians looking to complete training. The lab is typically deployed on-site for six to seven months while training is conducted and is equipped with industry-standard Amatrol learning equipment machinery and technology, including electro-mechanical trainers, control logic simulators, AC/DC systems, electric motor controls, laser shaft alignment and vibration analysis instruments.
Staying current in a competitive landscape is vital for any business and with a growing manufacturing sector, companies in the greater Lehigh Valley area are turning to LCCC and the mobile manufacturing lab to achieve their employee training goals. Currently, 10 Omnova, A Division of Surteco employees are working to complete the training with plans to graduate the program at the end of July, 2024.
They each attend four-hour hands-on training sessions in the lab before or after their shift under the supervision of trained instructors. Students learn ladder logic programming skills and troubleshooting on Programmable Logic Controllers as well as basic pneumatic systems. The benefits have been clear to Sarlat, “It’s critical. We intend to put all of our newly hired electro-mechanics (EMT’s) through this program because we found it to be that beneficial.” As a training partner, LCCC allows Omnova to save money as it alleviates the need to hire an in-house trainer or training equipment, while reaping the rewards of having a customized experience and increasing employee retention and recruitment. “It’s helping to keep us competitive as a business. We’re using it as a way to encourage people to come on board with us,” says Sarlat.
Don Worman, who heads up Specialty Manufacturing Training/Business Development at LCCC, notes the value to employers, “‘Bringing the college to the business provides vital training to the employees and minimizes the time the students (employees) must be away from the plant and off the floor. It’s a huge cost and time savings to the employer.”
Each industry is different and as such the college prioritizes a customized experience for every training partner, to ensure that training meets specific needs. Omnova was no different. According to Sarlat, “Every single person that I have worked with from LCCC has been very communicative, explains everything very clearly, has been super flexible, and very open to customizing the program.”
For more information on any of the three mobile manufacturing labs LCCC has available for customized training, visit the website.